ICD / ITKE Pavilion 2014-15
Individual Role: System Development, Fabrication & Construction.
The ICD/ITKE Research Pavilion 2014-15 demonstrates the architectural potential of a novel building method inspired by the underwater nest construction of the water spider. Through a novel robotic fabrication process an initially flexible pneumatic formwork is gradually stiffened by reinforcing it with carbon fibers from the inside. The resulting lightweight fiber composite shell forms a pavilion with unique architectural qualities, while at the same time being a highly material-efficient structure.
The design concept is based on the study of biological construction processes for fiber-reinforced structures. These processes are relevant for applications in architecture, as they do not require complex formwork and are capable of adapting to the varying demands of the individual constructions. The biological processes form customized fiber-reinforced structures in a highly material-effective and functionally integrated way. In this respect, the web building process of the diving bell water spider, (Agyroneda Aquatica) proved to be of particular interest. Thus the web construction process of water spiders was examined and the underlying behavioral patterns and design rules were analyzed, abstracted and transferred into a technological fabrication process.
The prototypical character of the fabrication process required the development of a custom made robot tool that allows placement of carbon fibers based on integrated sensor data. The technical development of this tool became an integral part of the architectural design process. The final tool allows for laying carbon fiber onto a dynamic membrane, which has not been developed previously within the industry. Through implementing sensors and integrating them into the general robotic system, a high level of precision of the process can be achieved.
During production nine pre-impregnated carbon fiber rovings are placed in parallel. 45km of carbon roving were laid at an average speed of 0.6 m min on 5km of robot path. This additive process not only allows stress-oriented placement of the fiber composite material, but it also minimizes the construction waste associated with typically subtractive construction processes.
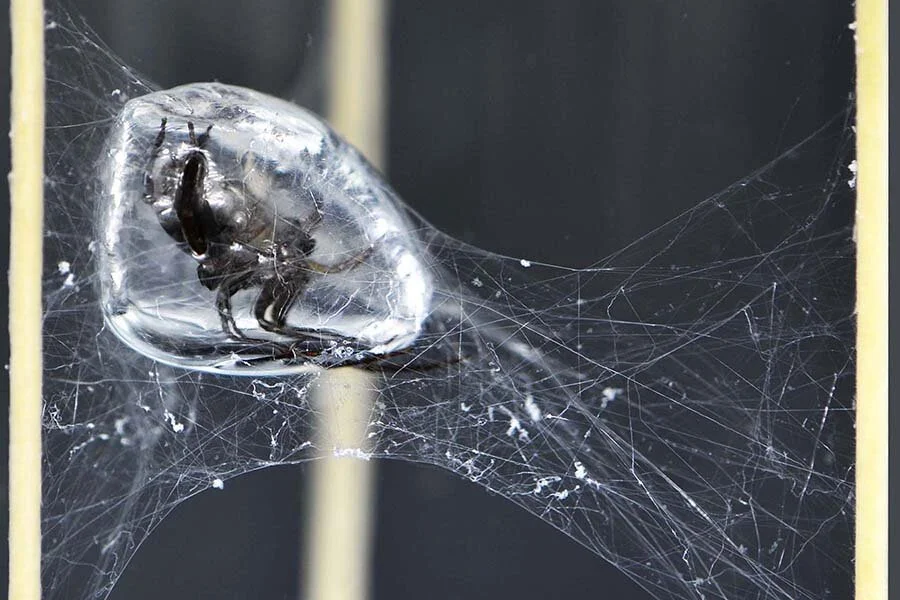
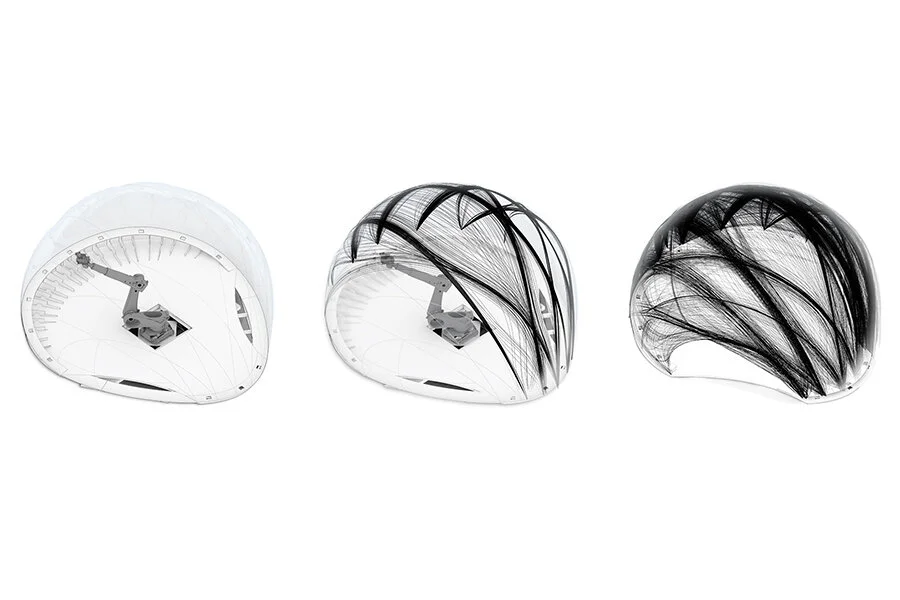
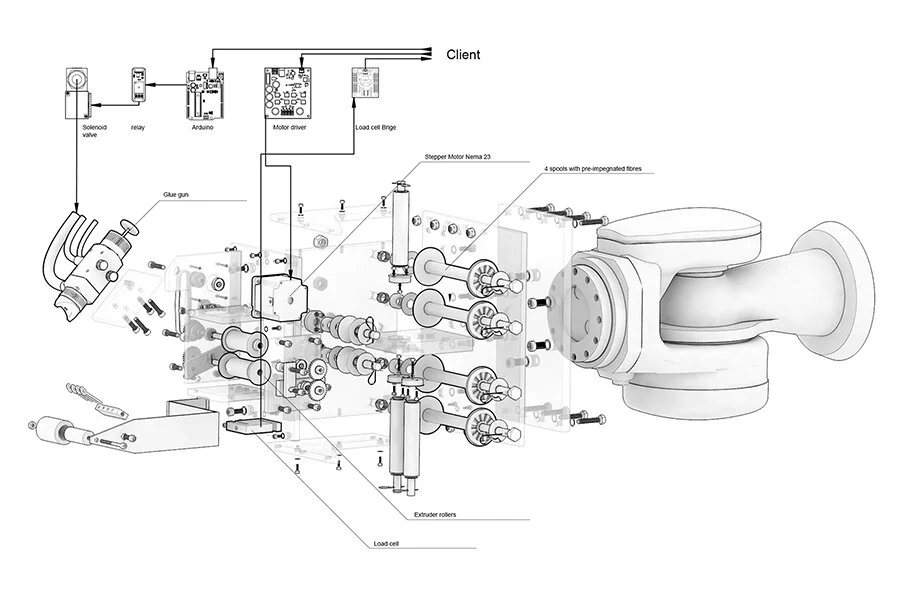
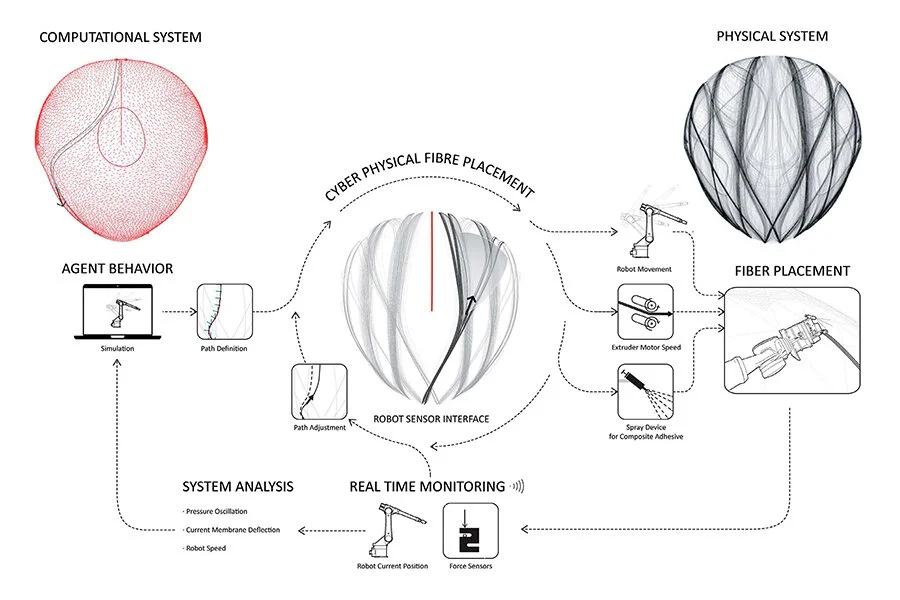