ICD Aggregate Pavilion 2015
Individual Role: System Development, Fabrication & Construction.
The ICD Aggregate Pavilion 2015 is the first architectural structure to be publicly realized with a designed granular system. It has been constructed and exhibited during summer 2015 in a central location at the University of Stuttgart, Germany. Designed granulates are defined as particle systems with large numbers, in which the individual granule is synthetically made and geometrically defined. Defining the geometry of the individual grain turns the aggregate into programmable matter, which has properties that cannot be found in naturally occurring granulates such as sand or gravel. Synthetic granular systems are an emerging area of architectural design research.
Whereas a wide range of possible granular behaviours can be programmed, the focus of the ICD Aggregate Pavilion 2015 has been the exploration of programmed verticality – a feature that transcends the natural granular angle of repose. Furthermore, the structures are functionally graded – using three different types of aggregates that can be deployed in different zones of the vertical structures to accommodate a load-transfer that increases from top to bottom. The system itself is fully re-configurable due to the fact that no permanent binding matrix is used.
The project has been developed at the Institute for Computational Design (ICD) over the period of a year. The structures themselves, as well as a range of possible construction and grading techniques, have initially been tested using scale models as well as one-to-one prototyping in a factory setting. These have been complemented by Distinct-Element Modelling (DEM) simulations which allow both for predictive and analytic modelling of particle systems with very high numbers. The cable robot was custom-designed as a large-scale robotic system that can easily be adjusted to changing site conditions and dimensions. After initial test-runs inside a confined framework, the system was adjusted to the site and fixed on four surrounding trees. On-site calibration allowed for precise deposition of the granular materials within the construction area of the robot. The structures could thus be constructed and re-constructed in situ.
Altogether 30 000 particles were injection-moulded using recycled plastics that were sourced from the local industry. Two to three geometric granule types, which are based on a single parametric model, were used in the construction to accommodate for different structural requirements. The entire structure was constructed in a few hours and re-configured multiple times during the exhibition period. No formwork is required during the construction process. The cable robot can have a maximum range of 30 metres, however, in this specific site the build-space was defined to be approximately seven by seven metres. It achieves accuracies in the range of a few centimetres with payloads of up to 10 kilograms.




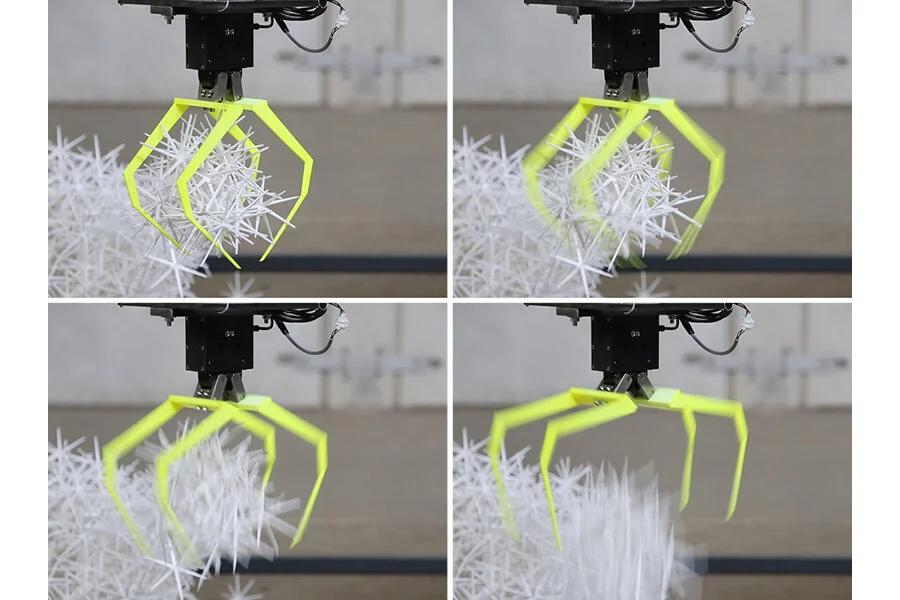
